HP Jet Fusion 3D Printers Target Production Applications

Latest News
May 17, 2016
While a lot of hoopla surrounding 3D printing surrounds empowering do-it-yourselfers and innovators with more accessible maker and prototyping capabilities, Hewlett-Packard is kicking it up a notch with the reveal of its first 3D printer that it hopes will revolutionize commercial manufacturing.
The HP Jet Fusion 3D Printing Solution, initially announced in October 2014, leverages HP technology to print at the individual voxel level (the 3D equivalent of a 2D pixel in traditional printing) enabling it to create higher performance, more industrial strength functional parts. The platform, aimed at model shops and 3D print service bureaus, addresses over 340 million voxels per second in a “one pass” printing method as opposed to competitors’ one point at a time printing approach. The result, HP claims, is radically faster build speeds—up to 10x faster than existing 3D printing technologies at half the cost.

Beyond prototyping applications, HP believes the price point and performance of the Jet Fusion platform makes it a viable alternative to traditional manufacturing practices for many production runs. The new technology is available in two models: The HP Jet Fusion 3D 3200, ideal for prototyping and short-run production, and the HP Jet Fusion 3D 4200, a higher-volume version designed to meet more robust production needs. Pricing on the 3200 model starts at $130,000 and will be available later this year, while the more expensive (pricing not announced yet) 4200 model will debut some time in 2017.

HP presents a challenge to existing additive printing technology like Fused Deposition Modeling (FDM) and selective laser sintering (SLS) through its ability to address individual voxels, which opens the door to all sorts of new applications, according to Terry Wohlers, principal consultant & president of Wohlers Associates, a consultancy focused on additive manufacturing and 3D printing. “Being able to address individual voxels will be big,” he said. “The technology can vary stiffness, flexibility (rubber-like properties), hardness, softness, surface texture, multiple colors and electrical conductivity—all within the same part.”
HP is also taking an open platform approach to its 3D printing play. The company has created a 3D material app store to promote materials for the new printer line and is initially collaborating with leaders in the materials space, including Arkema, BASF, Evonik and Lehmann & Voss, to supplement its initial support of nylon. Support for future materials like plastics, ceramics and metals will come over time, launched by HP or members of its ecosystem, officials said.
On the software side, HP is collaborating with partners like Autodesk Netfabb, Materialise, and Siemens to evolve their manufacturing and engineering design tools to better support 3D printing. Siemens PLM Software, for example, announced it was modifying its suite of design and simulation tools to take advantage of HP Multi Fusion technology’s advanced capabilities, including its voxel-level support.
Looking further down the road, HP says the voxel-level functionality, coupled with a future, expanded palette of materials and colors, will open doors to all sort of new applications by allowing unprecedented control and nearly limitless combinations. For example, users will be able to print sensors into parts, providing critical embedded intelligence for Internet of Things applications; or print information into parts, using color to call out visible and hidden information.
The HP Jet Fusion 3D 3200 and 4200 models are being touted as end-to-end solutions. The printer deposits powder from a print bar that looks similar to a scanning bar on a typical 2D printer, but it makes two fast area wide passes to achieve part production at top speed. The printer also supports a multi-agent fusing process, another design point to optimize performance. To facilitate easy clean up and to minimize materials usage, the printer is designed to use the recycled powder—up to 80% of material in some cases, HP officials said.
This video gets into the particulars of how the proprietary Multi Jet Fusion technology works.
Subscribe to our FREE magazine,
FREE email newsletters or both!Latest News
About the Author

Beth Stackpole is a contributing editor to Digital Engineering. Send e-mail about this article to [email protected].
Follow DE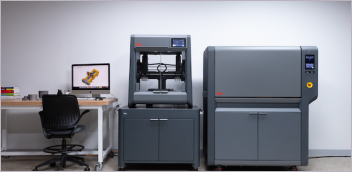
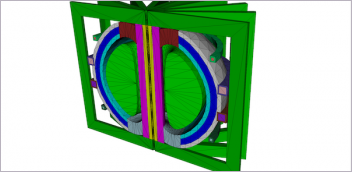
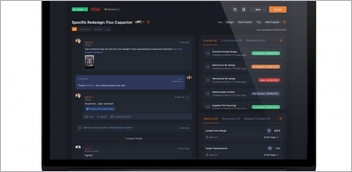
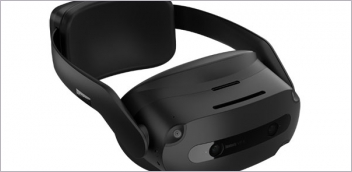