Power of Good Design
Applying emphasis on effective and innovative design processes in the design for additive manufacturing space can pay off and trim costs in the long run.

Danish manufacturer Advansor used DfAM techniques to redesign a heat pump part, resulting in a reduction in heat loss and an annual reduction of carbon dioxide emissions. Image courtesy of Teknologisk Institut.
Latest News
April 16, 2024
The design phase for any new project accounts for between 5% and 15% of total product cost. Decisions made during the design phase can have a profound impact on the rest of the product’s costs. Manufacturing methods, materials and logistics are all set in place. Good design can lead to efficiencies and savings in these areas, whereas poor design can result in increased costs down the line.
The cost-effectiveness of direct financial investment in the design phase can be disproportionately large. This leads many companies—especially in such competitive and complex industries as transportation and high tech—to place a strong emphasis on effective and innovative design processes.
In recent years, a new approach to design thinking has evolved. The maturing of 3D printing—now often known as additive manufacturing (AM)—has led to a newer industry term, design for additive manufacturing (DfAM).
“How one thinks about design changes when working with AM, one can concentrate more on functionality and less on manufacturability,” notes The 2024 Wohlers Report on AM from ASTM International.
This article explores simple questions with not-so-simple answers: How would product design change if “DfAM thinking” was applied to every new project? Could it be a method to generate the “outside-the-box” thinking engineers dream of but seldom achieve? Does thinking less about manufacturability and more about functionality make a worthwhile difference?
Digital-First Thinking
DfAM forces the engineer to wrestle with concepts not always a part of the typical manufacturing process. More than specific engineering decisions, DfAM means the entire process from initial concept to shipping is fully digital.
Below are seven aspects of DfAM that highlight what we might call “digital first” thinking. These advantages are not universal to every design project. They point to multiple advantages of looking at every project as if it is headed for AM.
- Complexity is free: In AM there is no real cost difference between creating a simple part or a complex part. Often the complex part uses less total materials. Traditional manufacturing methods often limit design complexity due to constraints in tooling or machining processes. In contrast, AM can produce intricate designs, including internal structures and complex shapes, without significantly impacting the cost.
- Customization is free: There are no cost penalties for custom (bespoke) production in AM. Every part can have a unique serial number permanently etched on the part; each orthotic device can be matched to a unique patient. Product ubiquity no longer lowers production cost.
- Built-in material efficiency: AM typically uses only the material needed to build the part, with minimal waste compared to subtractive and formative manufacturing processes. Not only does this save money on materials, it is also more eco-friendly.
- Light is right: DfAM enables the design of parts that are lighter yet still functional, which is especially beneficial in industries like aerospace and automotive. This is achieved through techniques such as lattice structures and topology optimization.
- Shorter supply chain: When several parts are redesigned as one, it has a ripple effect on manufacturing costs. Less tooling and less transport between factories are the most obvious benefits.
- Integration of function: Multiple parts (that would traditionally be manufactured separately and then assembled) can often be combined into a single, complex component. This not only reduces assembly time, but can also increase product strength and reliability.
- Built-in sustainability: Because DfAM often leads to less material waste and lighter products, it follows that there is less energy consumption caused by the product, which means a lower carbon footprint.
The Danish Digital-First Approach
There is an old saying, “Everybody talks about the weather but nobody does anything about it.” Now that weather discussions often refer to climate change, there are people trying to do something about it. A digital-first approach to this discussion comes from Denmark.
Danish AM Hub is a research and development consortium funded by private industry and government. It has published CO, a technology-agnostic carbon dioxide equivalent calculator. Manufacturers can use it to compare AM to conventional manufacturing techniques.
Danish manufacturer Advansor used the calculator to redesign an industrial heat pump part that was causing pressure loss issues. The DfAM approach along with use of the CO2e Calculator led to reduced part count from 17 to 3. Pressure loss was minimized with a new internal design that optimized flow. The new part provides a 1% energy savings per part. For their typical industrial heat pump, this results in an annual reduction of 70,000 kWh and 19,400 Kg of carbon dioxide emissions.
TRIZ to the Rescue
A research team of scholars from Iowa State University and Incheon National University have studied how to integrate AM into early design.
“Most existing DfAM methods do not effectively consider the capabilities of extant additive manufacturing technologies in the early design stages, and therefore it is hard to map functional requirements from customer needs onto a product design,” the researchers note.
The team devised a framework that integrates two well-known engineering methods, axiomatic design and TRIZ (a Russian acronym for Theory of Inventive Problem Solving).
The results? Such an integrated approach “is effective because the axiomatic design approach can be used to systematically define and analyze a design problem, while the TRIZ problem-solving approach combined with an additive manufacturing database can be used as an idea generation tool to generate innovative solutions for the design problem.”
Another research team (Pennsylvania State University) recently explored how the delicate balance between opportunistic and restrictive design can change when using DfAM. Instead of an either/or approach, the team notes DfAM requires designers to transition from a restrictive design for manufacturing mindset towards a dual-design approach.
Their findings suggest “introducing designers to [opportunistic DfAM] early [in their university training] could help develop a dual design mindset” as they often “demonstrate a greater use of certain DfAM concepts.”
The spectrum of benefits using DfAM. Image courtesy of Cati.com.
The Digital-First Pivot
People apply technology one wave of innovation at a time. Often, these waves overlap. It took years for CAD drafting to completely eliminate drafting tables. Model-based design is common, as is drafting. Now DfAM is nearing a tipping point. None of the previous waves were tsunamis; adopting DfAM as a common methodology won’t wipe out the past overnight. Yet the benefits are becoming obvious.
Moving to digital first, DfAM-inspired thinking requires a pivot from emphasizing functionality over manufacturability. In many companies, this will be challenging. The results will be significant. Liberating designers from traditional limitations means there is a new opportunity to engage product design with a built-in prioritization of innovation, sustainability and functionality.
Subscribe to our FREE magazine,
FREE email newsletters or both!Latest News
About the Author

Randall S. Newton is principal analyst at Consilia Vektor, covering engineering technology. He has been part of the computer graphics industry in a variety of roles since 1985.
Follow DE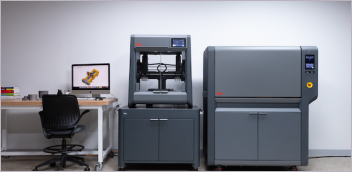
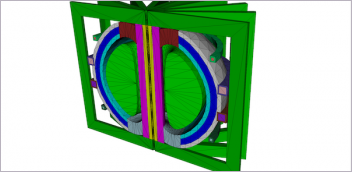
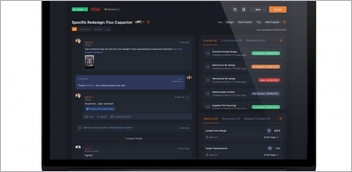
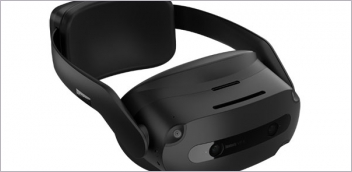