The Incredible Lightness of Printing Graphene

Latest News
March 8, 2016

Graphene aerogel is one of the lightest known materials and (according to those compulsive record keepers over at the Guinness Book of World Records) also the least dense solid.
Graphene may just be the “wonder” material of the century thanks to its strength, conductivity and flexibility. The aerogel form of the material is highly compressible and conductive and can absorb up to 850 times its own weight, which means it could potentially open up all sorts of new applications, like efficiently cleaning up environmental spills, energy storage, insulation and other uses.
Researchers from the University at Buffalo, State University of New York (SUNY), and Kansas State University have found a way to 3D print this light material. They published their research in the journal Small.
There are ways to 3D print aerogels by mixing them with polymers and then removing the polymer from the final object. This process can damage graphene aerogel structures, however.
Instead, the team mixed graphene oxide with water and then printed at -25°C. The ice in each frozen layer acted as a support for the aerogel structure, and was then removed using liquid nitrogen. In this way, they were able to remove the water without damaging the structure.
“Graphene is notoriously difficult to manipulate, but the structures we built show that it’s possible to control its shape in three-dimensional forms,” said Chi Zhou, assistant professor of Industrial and Systems Engineering at UB’s School of Engineering and Applied Sciences, and a corresponding author of the study.
According to the report, researchers were able to achieve densities of 0.5kg per cubic meter to 10kg per cubic meter. The team created lattice-shaped cubes and a three-dimensional truss with overhangs.
“By keeping the graphene in a cold environment, we were able to ensure that it retained the shape we designed. This is an important step toward making graphene a commercially viable material,” said Dong Lin, assistant professor of Industrial and Manufacturing Systems Engineering at Kansas State University.
Lawrence Livermore National Laboratory (LLNL) last year reported success in 3D printing graphene aerogels using an aqueous GO suspension and silica filler to create the ink. They burned off the silica using hydrofluoric acid.
You can see the freeze-casting process in action in the video below.
Source: University at Buffalo
Subscribe to our FREE magazine,
FREE email newsletters or both!Latest News
About the Author

Brian Albright is the editorial director of Digital Engineering. Contact him at [email protected].
Follow DE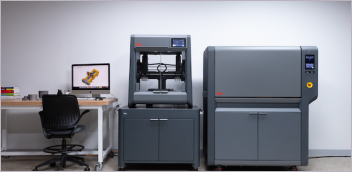
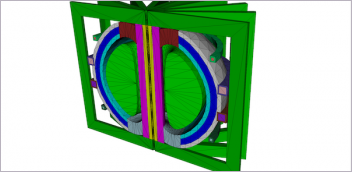
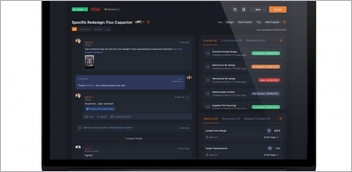
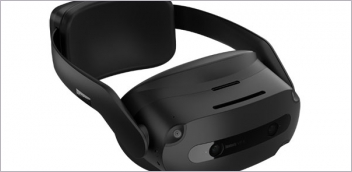