ESA Test Fires 3D Printed Thrust Chamber

Witness the 3D printed platinum thrust chamber, still shiny and chrome after repeated test firings. Courtesy of ESA.
Latest News
June 18, 2015
Any time you work with expensive materials, it’s important to do the most you can using the smallest amount possible. Savings from one project can help fund the next. Material savings is one of the big reasons additive manufacturing (AM) has drawn attention from businesses and organizations around the world.
The European Space Agency (ESA) has been experimenting with AM to construct a platinum–rhodium alloy thrust chamber. Priced at over $60 a gram, platinum is one of the most expensive materials used for aerospace manufacturing, but is highly prized for its durability. Recent test firings of a 3D printed platinum thrust chamber were successful, providing proof of concept.

“This is a world first,” explains Steffen Beyer of Airbus Defense & Space, managing the project. “The firings included a single burn of 32 minutes, during which a maximum throat temperature of 1,253°C was attained. It demonstrates that performance comparable to a conventional thruster can be obtained through 3D printing.”
The thruster was built using laser sintering. For those less familiar with the technology, during laser sintering one or more lasers are used to trace the outlines of the object to be built in a bed of powdered metal material. The powder fuses wherever the laser touches, slowly building an object in three dimensions as one layer builds upon the next.
The nature of metal 3D printing reduces waste to almost nil, meaning greater savings per part than could be accomplished through the use of standard manufacturing processes. AM also offers greater freedom of design than traditional manufacturing methods, which can offer additional savings by printing a complex design in a single piece, rather than producing it in multiple pieces that require additional assembly.
The prototype thruster was produced and tested at the Airbus Defense & Space facility in Lampoldshausen, Germany as part of ESA’s long-running Advanced Research in Telecommunications Systems program, ARTES. The successful test is a step forward on the road to total product qualification under ARTES specifications.
“Then, in the next phase, we will attempt to print using a new alloy, platinum–iridium, which has performance advantages,” said Beyer. “This alloy cannot easily be manufactured by traditional techniques like casting and forging, so printing is the only way it can be harnessed for space use.”
Below you can watch a clip of the thruster test firing.
Source: ESA
Subscribe to our FREE magazine,
FREE email newsletters or both!Latest News
About the Author
John NewmanJohn Newman is a Digital Engineering contributor who focuses on 3D printing. Contact him via [email protected] and read his posts on Rapid Ready Technology.
Follow DERelated Topics
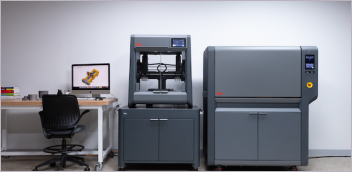
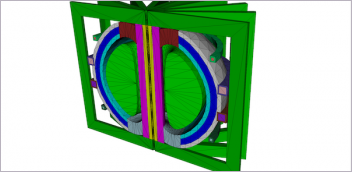
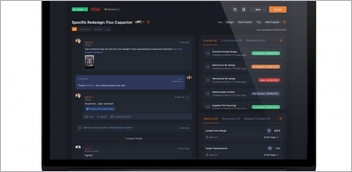
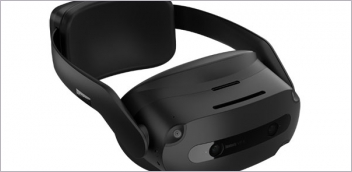