American Process Partners with ORNL to Research More Durable 3D Printing Resin

These tiny strands of cellulose could be the key to strong AM parts. Courtesy of American Process.
Latest News
June 1, 2015
Much of additive manufacturing (AM) involves a tradeoff of some kind. Objects printed with plastic filament trade fine detail for affordability. Items printed with resin offer improved detail at the cost of durability. Choice of material, and thus which printing process is used, generally comes down to the end use of a printed object.
A new partnership between American Process and Oak Ridge National Laboratory (ORNL) offers the potential to bridge the gap between the fine detail offered by resin and the durability of plastic. The partnership was formed to conduct research on a new material for use in AM called nanocellulose. The new material is expected to be strong, lightweight, inexpensive and environmentally friendly.

“This new eco-material can both substitute and enhance the performance of petroleum-based plastics in an environmentally friendly and market competitive way,” said Theodora Retsina, CEO at American Process. “Carbon fibers are extremely strong and light but expensive to produce … Nanocellulose has even lower weight than carbon fibers and is just as strong. With our manufacturing breakthrough, nanocellulose is a fraction of the price of carbon fibers.”
Cellulose, you may remember from biology class, is a naturally occurring organic material generally found in tree trunks. By itself, cellulose is a strong natural material, thanks to densely cluttered hydrogen bonds. Nanocellulose is derived from wood and its natural durability is improved upon in the production process making it as tough as Kevlar.
“Cellulose is the most abundant natural organic material on Earth and it’s renewable and compostable,” added Retsina. “We didn’t invent nanocellulose, we made it less expensive, more thermally stable at high temperatures, and gave it functionality to blend with hydrophobic polymers – thereby enabling market applications and opening the road to commercial production.”
The partnership was estblished to create a new nanocellulose resin for use in AM systems. The new material has a large number of potential applications, including replacing carbon fiber parts in cars with stronger, lighter and less expensive parts. According to American Process, the price for the new material should be on par with existing polymers, and it could begin shipping as early as the fourth quarter of this year.
Below you’ll find a video about nanocellulose.
Source: PRWeb
Subscribe to our FREE magazine,
FREE email newsletters or both!Latest News
About the Author
John NewmanJohn Newman is a Digital Engineering contributor who focuses on 3D printing. Contact him via [email protected] and read his posts on Rapid Ready Technology.
Follow DE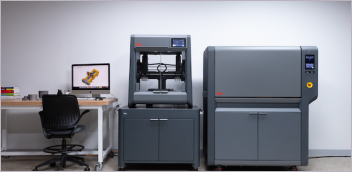
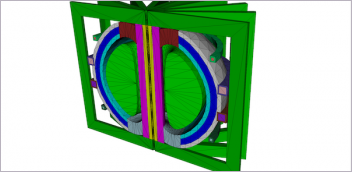
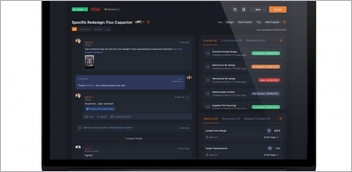
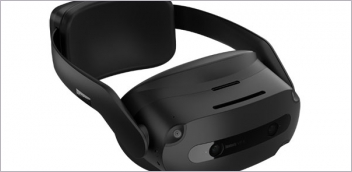