Additive Manufacturing to Assist with Diabetes Monitoring

A closeup look at the diabetes sensor being developed by OSU. Courtesy of Greg Herman.
Latest News
March 31, 2015
If you are looking for a single field that has experienced a boom since adopting additive manufacturing (AM) you could do worse than to focus on medical. Leaving aside bioprinting, which is still in its infancy, AM allows doctors to prepare for difficult surgeries by producing accurate models. 3D printing has also been responsible for a number of technological breakthroughs in medical equipment.
Researchers at Oregon State University (OSU) have recently developed an improved glucose sensor for patients with Type 1 diabetes. The sensor is part of a monitoring system that should be less expensive and more comfortable for patients.

Diabetes is a growing health concern around the world affecting an estimated 387 million people in 2014, according to the International Diabetes Federation. The number of people suffering from diabetes is expected to rise to 592 million in the next two decades. Currently, the global price tag for dealing with the disease adds up to $612 billion.
The sensor developed by OSU would act like an artificial pancreas, to monitor blood glucose levels. When paired with portable infusion pumps, the entire system can assist patients by maintaining proper levels of glucose with controlled delivery of the hormones insulin and glucagon. Additionally, the sensors are thin enough they can be wrapped around a catheter.
The sensor is built using conductive e-ink and a plastic substrate. The new system is less intrusive, requiring a single entry point rather than the usual four, which results in greater comfort for users. Because the sensor is built using AM, each unit can be produced more quickly and with less waste than existing sensors.
“These are disposable devices that only last about a week and then need to be replaced,” said Greg Herman, an OSU associate professor of chemical engineering. “Some other approaches used to make them might waste up to 90 percent of the materials being used, and that’s a problem in a throw-away sensor. It’s also important to keep costs as low as possible, and printing systems are inherently low-cost.”
Below you’ll find a short video explaining diabetes using 3D printed protein models.
Source: OSU
Subscribe to our FREE magazine,
FREE email newsletters or both!Latest News
About the Author
John NewmanJohn Newman is a Digital Engineering contributor who focuses on 3D printing. Contact him via [email protected] and read his posts on Rapid Ready Technology.
Follow DE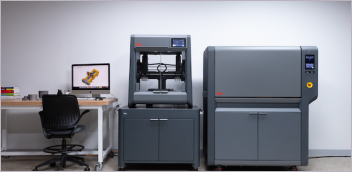
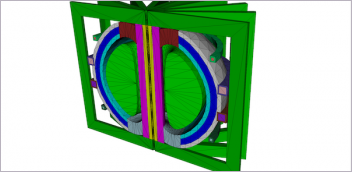
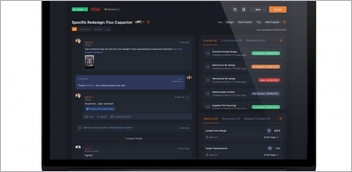
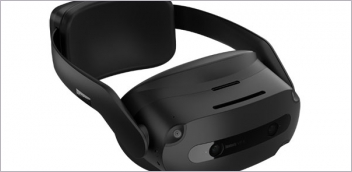