DMG MORI Hybrid System Combines Additive and Subtractive Manufacturing

DMG MORI’s new hybrid manufacturing system leverages both additive and subtractive processes. Courtesy of DMG MORI.
Latest News
October 27, 2014
Since the technology hit its stride, additive manufacturing (AM) has offered new manufacturing options. Simply put, AM can produce parts that no other system can. The one sticking point has been production speed. While a few high production type AM systems have appeared, such as the one developed by 3D Systems for Project Ara, in general subtractive manufacturing is still the king of mass manufacturing.
Most critics agree that AM will eventually catch up, but until then many companies still rely on more traditional manufacturing methods. DMG MORI has launched a new system that looks to combine the flexibility offered by AM with the speed characteristic of subtractive manufacturing with its LASERTEC 65 3D.

From DMG MORI’s website:
Up to now additive technologies have been used to generate prototypes and small parts. By combining both, additive manufacturing via powder nozzle and the traditional cutting method in one machine, totally new applications and geometries are possible. Especially large workpieces with high stock removal volumes are now possible to be machined in an economical way. The flexible change between laser and milling operation allows the direct milling machining of sections which are not reachable anymore at the finished part.

The LASERTEC 65 3D combines laser sintering with a 5-axis milling machine to offer a system capable of producing complex shapes at a rapid pace. The system employs a powder nozzle and laser process to build objects via sintering with a wall thickness between 0.004 and 0.2 in. Depending on the part, build times can be enhanced by a rotating build plate. Once a section has cooled, it can be machined by switching to the 5-mill axis.
The hybrid system takes advantage of AM for more than just the initial build. The laser sintering system is capable of adding additional details to a part that has already been built, or to damaged parts. This allows the system to produce a finished product in one piece, rather than multiple pieces that require additional labor or machining to complete. The process also offers the freedom to build features such as overhanging contours without requiring support structures.
DMG MORI’s new system is capable of working with a variety of materials, including stainless steel, tool steel, aluminum and aluminum alloys, bronze alloys, precious metal alloys, copper alloys, and stellite. Below you’ll find a short video demonstration of the capabilities of the LASERTEC 65 3D.
Source: DMG MORI
Subscribe to our FREE magazine,
FREE email newsletters or both!Latest News
About the Author
John NewmanJohn Newman is a Digital Engineering contributor who focuses on 3D printing. Contact him via [email protected] and read his posts on Rapid Ready Technology.
Follow DE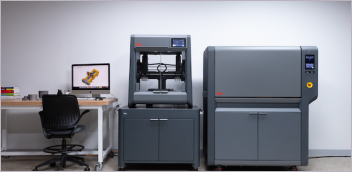
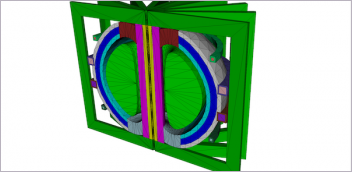
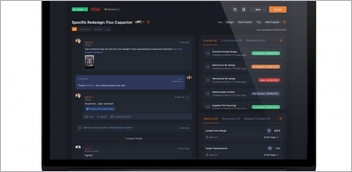
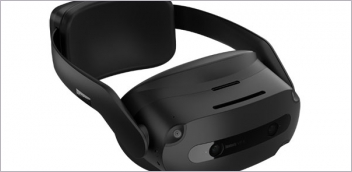