New Research Paves the Way for Gradient Metal Additive Manufacturing

Scientists make a rocket nozzle using a new 3-D printing technique that allows for multiple metallic properties in the same object. This technique involves blowing multiple metal powders into a laser beam, so that the laser melts the powder and forms a small pool at the point where the laser touches the part that is being built. Courtesy of Nasa JPL/CalTech.
Latest News
July 30, 2014
While Amazon will likely be grabbing the majority of additive manufacturing (AM) news for the near future, other, even more dramatic developments are taking place outside the consumer side of AM. And where it’s likely most of the doo-dads ordered from Amazon will be built from one kind of plastic or another, today’s big news comes from the metal end of the AM materials field.
A research team comprised of individuals from the Jet Propulsion Lab, the California Institute of Technology, Pasadena, and Pennsylvania State University, University Park, have come together to develop a method of building gradient metal objects. This will allow manufacturers and designers the freedom to design and produce parts in which the metal within a single part changes based on specific requirements.

This is an important step forward for AM, as the authors of the research paper explain:
“Since the development of AM in metals, much of the research and technology development has focused on reducing manufacturing costs (relative to conventional machining), fabricating parts that cannot be easily machined using other techniques, and qualifying parts fabricated by AM to verify compliance with existing material standards.
“One of the most beneficial applications of AM with metals, however, is the ability to create net-shaped parts with custom compositions. The LD process is ideally suited to create these alloys, owing to the ease by which different elemental or alloy powders can be introduced into the melt pool during the fabrication process.”
Why all the fuss over gradient materials? Assume you were designing a new aerospace part that needed to be strong, light and heat resistant. Any number of metals or alloys could fulfill one or maybe even two of those requirements in a single part (no welds), but probably not all three. The ability to create a part from heat resistant materials on one part of the structure, that is contained within a tough shell, and is still light enough to be valuable for aerospace applications opens up many possibilities.

The new process works by building the desired object on a rotating surface. A laser is used to deposit material on the surface as it rotates, drawing materials from four powder blowers. The process not only allows for the manufacturing of gradient materials, but can also include specific alloys on the fly. The presence of four blowers also reduces the need to change out materials, making for a faster and more even build process.
The research study, titled “Developing Gradient Metal Alloys through Radial Deposition Additive Manufacturing” can be found at nature.com.
Source: Jet Propulsion Laboratory
Subscribe to our FREE magazine,
FREE email newsletters or both!Latest News
About the Author
John NewmanJohn Newman is a Digital Engineering contributor who focuses on 3D printing. Contact him via [email protected] and read his posts on Rapid Ready Technology.
Follow DERelated Topics
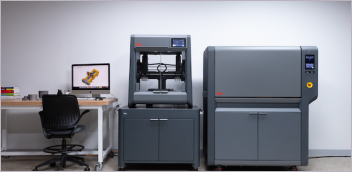
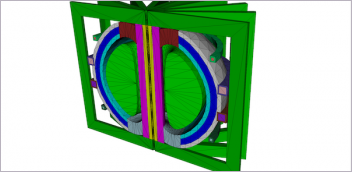
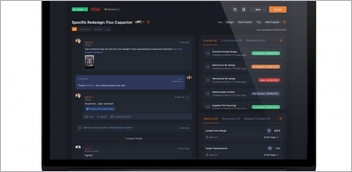
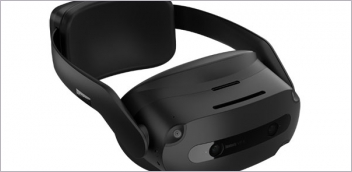