Lockheed Martin Pushes Forward on Additive Manufacturing for Satellite Construction

The A2100 satellite may consist of 50% 3D printed parts by 2017. Courtesy of Lockheed Martin.
Latest News
July 28, 2014
If it flies, drives, or sometimes even walks, additive manufacturing (AM) is probably involved (or will be). In the course of what seems like just a few years, AM has gone from a tool mainly used for rapid prototyping to a powerful, versatile force in manufacturing. Lockheed Martin is just one among dozens of companies that have seen the potential of AM and have invested company resources to leverage the technology more efficiently.
Lockheed Martin recently redesigned the A2100 satellite, which has been used for telecommunications since the 1990s. Part of the redesign involved updating the electronics and power systems, along with a reduction in the overall number of parts required to build the satellite. Reducing parts makes the satellite less expensive to produce and reduces its weight. Part of the new design incorporates 3D printed parts. The overall savings in parts is near 60%.

A complete description of the A2100 can be found on Lockheed Martin’s website:
This modular geosynchronous satellite has a design life of 15 years and a flexible payload capacity ideally suited to meet the demand for commercial space systems well into the 21st century—a demand driven by growth in mobile telephony, business services, direct broadcast, internet, multimedia and broadband services.
The current design of the A2100 features just 10% 3D printed parts, but the company is certain that number could rise to 50% in the next three years. As an example of the time that can be saved by building parts using AM rather than more traditional methods, Lockheed Martin reports that some brackets can take as long as 30 hours to produce a single finished part when machined. An AM system can produce 300 of the same bracket in a single day.
Part of Lockheed Martin’s incentive to reduce the weight of the A2100 can be put down to simple logistics, but the company’s recent deal with the US Air Force might also have been a factor in the redesign effort. Lockheed Martin has been selected as part of the Air Force’s Hosted Payload Solutions (HoPS) program, which will offer space on commercial spacecraft for government sensor and electronic packages. The HoPS program is backed by a $495 million budget and the A2100 redesign seems almost tailor-made for inclusion.
Below you’ll find a video in which Lockheed Martin discusses AM and related materials.
Sources: Lockheed Martin, Aviation Week
Subscribe to our FREE magazine,
FREE email newsletters or both!Latest News
About the Author
John NewmanJohn Newman is a Digital Engineering contributor who focuses on 3D printing. Contact him via [email protected] and read his posts on Rapid Ready Technology.
Follow DE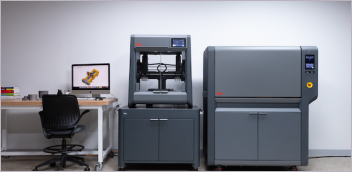
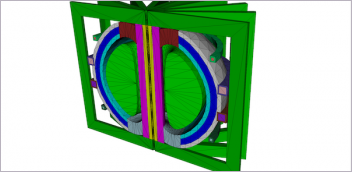
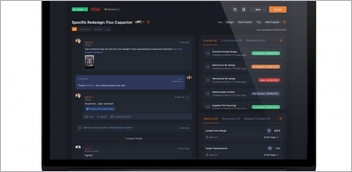
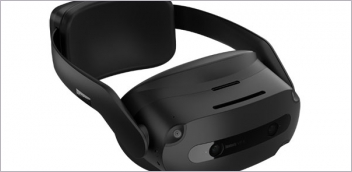