
This rendering of titanium spinal implants shows how the pores in the implants, created with software from WITHIN, reduce weight and promote osseointegration. Courtesy of WITHIN
Latest News
October 10, 2013
Build envelope and material availability are key parts of additive manufacturing (AM), but design flexibility is its core. The power to build three dimensional objects of nearly any shape, complete with complex internal geometries, is what gives AM a leg up over traditional manufacturing methods.
In most cases, this flexibility of design means working with 3D modeling software of some kind, and as the AM industry advances, these design programs become increasingly more sophisticated and specialized. To meet the demands of AM design in the medical field, C&A Tool and WITHIN have launched a metal-implant design and manufacturing program called WITHIN Medical.

WITHIN Medical is targeted at medical, surgical, and orthopedic designers and manufacturers, offering the flexibility to design patient-specific implants that, according to the companies involved, help to encourage osseointegration or bone growth. Once a design is complete, the implants are built using direct metal laser sintering (DMLS).
“With this program, companies now have the opportunity to explore the benefits that designing for DMLS can bring to their medical products—without investing in their own laser-sintering system,” says John Halverson, medical business unit manager at C&A Tool. “Through this technology, they’ll be able to discover firsthand how DMLS reduces manufacturing steps, improves product performance and allows them to tailor medical products to individual patient needs.”
Traditional manufacturing methods produce an implant that still requires plenty of secondary finishing before it is ready for use. DMLS reduces or eliminates the need of secondary finishing steps by determining the porosity, texture and density of an implant as it is being built. Density control also makes manufacturing the implant to a specific weight simpler.
The move to AM to build implants also gives doctors the opportunity to design each implant specifically for each patient. Rather than being forced to work with predetermined sizes, medical care specialists can utilize WITHIN Medical to design patient-matched spinal reconstructions, acetabular cups, tibial trays, and other parts from MRI or CT scan data.
To support its new service, C&A Tool has invested in six EOS DMLS systems (both EOSINT M 270 and M 280). EOS AM systems are capable of working with a number of different systems biocompatible materials, such as medical-grade titanium (Ti64) cobalt-chrome, and stainless steel alloys.
The WITHIN Medical software is free to download and use, and offers protection for proprietary digital models as they are passed between designers, OEMs, service bureaus, and contract manufacturers. It can assist designers in determining variable density, porosity, and final texture of an implant.
You’ll find a video overview of the program below.
Subscribe to our FREE magazine,
FREE email newsletters or both!Latest News
About the Author
John NewmanJohn Newman is a Digital Engineering contributor who focuses on 3D printing. Contact him via [email protected] and read his posts on Rapid Ready Technology.
Follow DE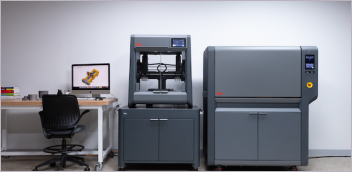
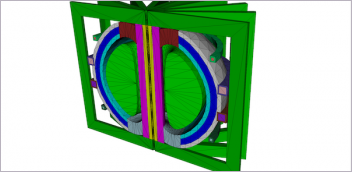
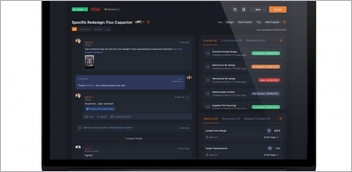
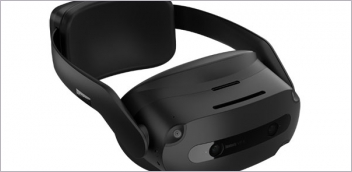