Mixing Metals via Additive Manufacturing Speeds Use of Molds and Dies
Latest News
September 10, 2012
Researchers at Swinburne University of Technology in Australia have found a way to slash the time it takes to make components out of aluminium and other metals by fine tuning the metals used in direct metal deposition (DMD) additive manufacturing (AM) systems. By using copper and tooling steel, researchers say they can cut cooling times of molten aluminum as it’s cast into molds. Traditionally aluminium components, such as those used in motor vehicles, are cast into a steel die or mold. The molten aluminium takes considerable time to cool down, and the component cannot be removed from the mold until it had cooled and hardened.
Swinburne Ph.D. graduate Khalid Imran and his supervisor Professor of Advanced Manufacturing at Swinburne’s Industrial Research Institute, Syed Masood, have combined the use of a giant 3D printer from Precision Optical Manufacturing (POM) Group and layering metals to make a predominantly copper mold that is promising to significantly reduce waste and cut cooling times in high-pressure die-casting by 33%.
“In the competitive manufacturing industry, time equals money, particularly in Australia where wages and energy costs are high compared with countries such as China and India,” Imran said. “If the production rate is high then you can produce millions of parts in a very short time and that will reduce the cost of manufacturing.”
Imran said that while tooling steel tends to hold heat, another metal — copper — is quick to release it. But the problem he found with copper was that it had a lower melting point than tool steel and when used as a mould interacted with the molten metal injected inside.
Working closely with the POM Group, designers and builders of DMD additive manufacturing systems, and Jyoti Mazumder, director of the Center for Laser-Aided Intelligent Manufacturing (CLAIM) at the University of Michigan, Imran found a solution: sandwiching a third metal that mixes with both copper and steel in between. The make-up of the bonding metal is a closely guarded secret.
Imran used the additive manufacturing process of DMD to layer the three metals and produce a predominantly copper mold. The concept makes a mold directly from powder, ribbon or wire deposited in layers, without the need for casting, forging, rolling, cutting, machining, welding or drilling.
At Swinburne, DMD is produced using a machine manufactured by the POM Group that is fed by up to four different metal powders and builds 3D items from scratch.
“The process particularly lends itself to making molds for die-casting, as the die cavities tend to be very complex and DMD provides a true metallurgical bond,” said Professor Masood.
“We have measured the quality of the parts produced and we have proven that the quality of the parts produced by bimetallic tooling is as good as the original tooling methods,” he said.
As well as being able to lay down multiple metals in complex patterns, the process has a major advantage over traditional tool making — it creates little to no waste.
Professor Masood said the technology would provide opportunities for companies to address needs in tooling development, tool and metal component repair, surface modification and coating, new alloy development and direct metal prototypes.
Below is a video showing POM Group’s DMD IC106 system in action.
Source: Swinburne University
Subscribe to our FREE magazine,
FREE email newsletters or both!Latest News
About the Author

Jamie Gooch is the former editorial director of Digital Engineering.
Follow DERelated Topics
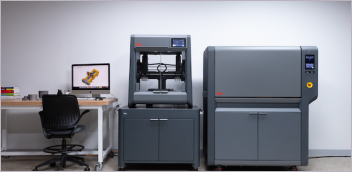
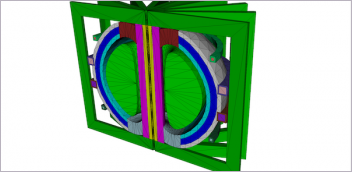
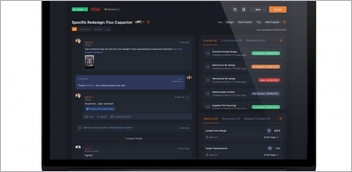
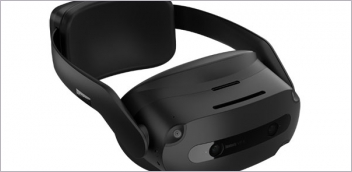