Latest News
May 26, 2012
If ever I wished I could clone myself, it had to have been during the Additive Manufacturing Users Group (AM-UG) Conference last month. Begun in 1988 as the SLA Users Group but newly expanded to include all types of AM technology, this event was a fantastic opportunity to gain an “in the trenches” perspective on the field from everyday system users; if only I could have attended every talk of the parallel sessions.
The morning presentations provided terrific overviews on topics ranging from what it will take for industry to establish AM as a production process to the latest activities of the ASTM-42 AM standards group. Two well-known names in the field presented the World Report (SLM Solutions’ Stefan Ritt) and the European Report (rapid-manufacturing consultant Graham Tromans) while consultant Todd Grimm presented a keynote speech urging attendees to question everything about how they’ve done AM in the past and could change things in the future.
Some interesting news items I gathered:
- Objet Geometries says they’re adding 39 new materials this month (perhaps some new blends) for a total of 107 materials; also, you can upgrade Eden systems to become Connex systems.
- Cornell University and Objet Geometries are working together to use VoxCAD software to simulate the behavior of models built in one piece with Objet's range of materials.
- Service bureaus are seeing more interest, knowledge and use of high temperature PEEK materials as well as flexible materials.
- ALM Engineered Materials says its company can modify a powdered-nylon material with different filler materials such as hollow glass spheres or carbon fibers and supply it in 2 to 3 days.
- The ASTM F42 group has a new working group addressing Directed Energy Deposition (LENS, Optomec).
- Renishaw is offering a 1KW laser on its (MTT) AM250 system.
- The Netherlands research organization TNO has a research project involving UV-curable resin with 30 micron droplets, forming parts on a continuous belt (like a conveyor belt) to build long parts.
- Objet is investigating and recommending a post-processing surface-quality treatment involving white-light photo-bleaching for parts made with its Velo Clear material.
Jeff DeGrange of Stratasys gave a nitty-gritty keynote speech on the steps needed to move more AM technology applications into a full production process. He says engineers would like to see more third-party test labs that could work with large part samples, and sees the following needs to happen:
- Establish process considerations such as: which tip would you use for a Stratasys FDM system? For an SLA system, what if a laser goes out — do you have a process to calibrate it for new parts?
- What will you require for part support design? What rules will you use for part nesting? How will you define secondary processes such as finishing, bonding, painting and joining?
- Come up with a defined approach for equipment repeatability, test coupons, throughput, scrap rate and material recyclability.
- Create a business process for your supply chain: Do you have multiple material sources? What system do you have in place for material traceability? What about data security and data management?
Lastly, Todd Grimm and Kevin Ayers (ask him about working for the FBI) took a team approach to sharing a check-list that is worth its weight in gold: topics to keep in mind and evaluate before buying an AM system:
- Understand your company’s products, customers, expectations for the AM system, required timeline (from purchase to part production) and available physical facilities (such as floor space).
- Have a benchmark part made by several AM system vendors — and don’t let the vendor pick the part!
- Get references of other customers who use the system in a similar way and go visit them.
- Reach out to experts for guidance (pros and cons). Ask questions and listen, listen, listen.
- Attend user-group meetings, especially AM-vendor-specific meetings.
- Compare facts to requirements: Will the material properties perform to your needs? Can you provide (if needed) compressed air, power requirements, floor space, curing oven, etc.? Who will do (and take) training? Who will be in charge of maintenance, upgrades and scheduling?
- Prepare a budget and ask for quotes that address: machine, materials, recurring costs (cleaning supplies), support/post-processing equipment, delivery dates and training.
- Once the system is in place and running, use it — try everything and don’t let it sit idle.
A nice plus to this event: the food and camaraderie were at a level of excellence unlike any I’ve encountered at professional conferences over many years (kudos to Gary Rabinovitz, Tom Sorovetz, Tim Gornet and the whole friendly team). The exhibit hall, too, seemed just the right size to encourage one-on-one conversations with all the vendors.
But perhaps the best part of the AM-UG experience is coming away with dozens of new contacts who are eager to keep sharing their advice with both newbies and “dinosaurs” alike. Next year’s meeting will be April 14-18 in Jacksonville, FL; mark your calendar and stay tuned at www.additivemanufacturingusersgroup.com.
Subscribe to our FREE magazine,
FREE email newsletters or both!Latest News
About the Author

Pamela Waterman worked as Digital Engineering’s contributing editor for two decades. Contact her via .(JavaScript must be enabled to view this email address).
Follow DE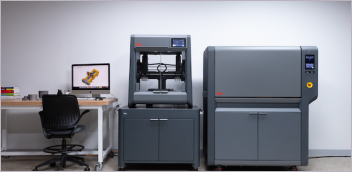
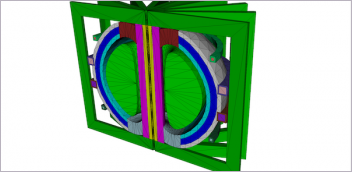
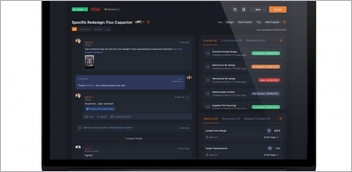
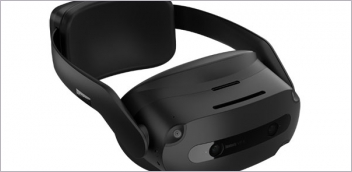