Maxifab Offers Scale Flexibility for 3D Printers

Maxifab scalable 3D printer case design. Courtesy of Ryan Robinson.
Latest News
April 27, 2012
Kickstarter is pretty awesome. It harnesses the power of the Internet and the creativity of small businesses or individual inventers to develop and manufacture products that larger companies might not ever take a risk on. And why shouldn’t it? The Kickstarter model reduces some of the risk of designing a new product.
Rather than hoping you can persuade your audience to buy a product with advertising or hoping your company can tap into a particular market, the Kickstarter process comes with built-in cheap market research. If people are interested in your product, they’ll pony up the cash to see it built. If no one is interested, the product will never see the light of day.
“Isn’t this an additive manufacturing (AM) blog?” is what you may be asking right about now. I’m getting to that. Kickstarter innovations are touching on AM in a number of ways. You have people trying to sell various types of hobbyist 3D printer models, while other folks work on what might be called AM peripherals (you can find our coverage of one example here).
One of the issues still faced by AM is that of scale. While it is true that you can build nearly anything with a 3D printer, you are limited by the build envelope you have to work with. In the case of most hobbyist printers, this is fairly small. The MakerBot Replicator has an envelope of 8.9 x 5.7 x 5.9 in. (or 225 x 145 x 150mm) and looking for larger envelopes vaults a customer into the range of industrial 3D printers that cost far more than most individual are going to pay.
Maxifab is a Kickstarter project that hopes to alleviate some of the issues with scale. Envisioned by its creator, Ryan Robinson, Maxifab isn’t just another DIY 3D printer kit. Rather than a set build envelope, Maxifab is designed to allow the user to decide how big of a 3D printer is required for their needs, and give them the tools to build it.
I think it’s a revolution in 3D printer design essentially giving the tools to generate your own 3d printer to your specifications, so you can bring your dreams to life. Simple construction, robust design, and design flexibility to build to the print envelope you want. Not just whats out there. –Ryan Robison, creator of Maxifab
The idea works by using a small set of plastic parts that perform multiple roles for a 3D printer. These parts are standardized and can be slotted into any size printer case the customer desires. Robison has designed the system so that the extruder head does its work on the x and y, while the build plate moves the z. According to him, this reduces inaccuracies in larger prints.
Maxifab reached its Kickstarter goal on April 15 and is set to go into production. For people uninterested in designing their own case, a standard DIY case can be purchased for the printer.
Below you’ll find a short video demonstrating the Maxifab’s process.
Source: Maxifab
Subscribe to our FREE magazine,
FREE email newsletters or both!Latest News
About the Author
John NewmanJohn Newman is a Digital Engineering contributor who focuses on 3D printing. Contact him via [email protected] and read his posts on Rapid Ready Technology.
Follow DE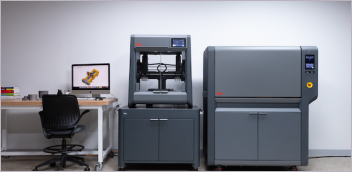
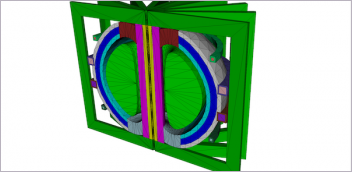
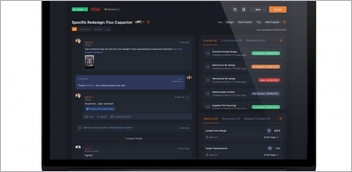
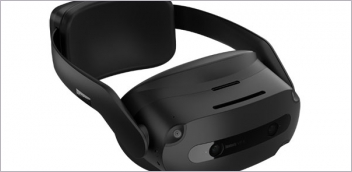